大企業という大船から降り、自らの手で小船を漕ぎ出す。
穏やかな海であれば小船でも乗り越えられるかもしれない。
しかしひとたび海が荒れると、沈没の恐怖と戦わなければならない。
そのプレッシャーたるや尋常ではないという。
半導体の接合装置などの開発を手がけるボンドテック。
2004年にスタートしたベンチャー企業だが、創業者の山内朗社長は
「やめたいと思ったことが何度もある」と語る。
そうしたなかでも画期的な技術をベースに製品を次々と開発。
創業からわずか5年にして、業界でも注目の企業へとのし上りつつある。
山内社長を支えているものは何なのか。
男のロマンを聞いた。
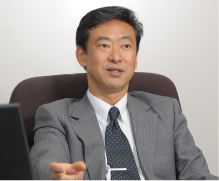
理想の3次元積層化技術を目ざして
2009年初夏、それはボンドテックの山内社長にとって新たな1ページとなった。販路を拡大すべく、丸紅情報システムズと販売代理店契約を結んだのだ。
「これまで半導体業界は、電子回路の配線パターンの微細化を進めながら成長してきました。1つのデバイスに多くのトランジスタを配置し、高性能化、コストダウン化をはかってきたのです。しかし、これ以上の微細化は、物理的に乗り越えられない壁が存在します。さらに既存生産方式で進んでいくには、製造装置の価格高騰も大きな障壁と言えるでしょう。この先、高性能化により半導体業界が成長を続けるためには、新しい技術として電子回路の3次元積層化が要求されています。またMEMS(Micro Electro Mechanical System)の分野では、新たなニーズを具現化するために、新しい手法が必要です。私は、新しい技術で次世代を担う分野を創造したいと思い、会社を作ったのです」
電子回路を大規模化するために、横に並べると面積が広くなってしまい、回路を接続する配線も長く、スピードが落ちるなどのロスが生じる。「3次元積層化技術」は複数の電子回路が形成されたチップやウェハを積層、つまり重箱のように垂直に積み重ねる技術である。面積は変わらず、配線の長さも積層されたウェハやチップの上下間で接続することで短縮が可能となり、計算処理の高速化も実現できる。また、既存の製造設備を活かしながら高性能化を実現する、具体的な手法だ。半導体製造ラインにウェハやチップを貼り合わせる装置を導入するだけで可能となる。半導体の3次元化の実現は「貫通電極」という技術により加速した。電子回路同士を上下に積層するためには、電極を上下間でつなぎ電気を結線することが必須となる。貫通電極は、シリコンウェハに微細な穴を開けて電極材料を埋め込む技術で、これにより接合の電気的な課題を解決すると見られている。
新たな分野「MEMS」
また、センサやバイオの分野で実用化が始まっているMEMS技術。これは半導体製造技術を活用した微細加工による、微小機械構造を搭載するデバイスのことだ。可動部を持つ圧力センサや、ジャイロセンサなどは、すでにカメラや車、ゲーム機器に搭載され活用されている。また、微小な流量で血液検査ができるなど、バイオメディカルの分野にも適用されつつある。MEMSデバイスはマイクロレベルの微小な構造物であり、いわゆる半導体素子と呼ばれる2次元的な回路ではなく、3次元的な立体構造である。しかも、可動する機械的要素の部品と、そのMEMS部が発するセンシング情報を受け取り、制御・コントロール信号に変換、発信する電気的要素の回路と、2つの要素で構成されている。
これらを一体化し、1つにパッケージ化するためには半導体とMEMS間での接合が必要となる。MEMSのガラス封止には現在多く採用されている接合方法が陽極接合※1 である。「陽極接合は、ガラスとシリコンウェハを張り合わせるための、高温、高電圧を必要とする接合方法です。ただし、異種材料間での接合のため、高温での熱膨張差によるソリやヒビ割れが問題となる場合があります。また、MEMSデバイス特有の要求仕様として、可動部を真空封止しなければならないという条件があります。可動部の真空度を保つため、接合した後、内部のガス発生をいかに防ぐかが、課題となっていました」
※1 陽極接合
アルカリガラスとSiを400度程度の加熱のもと、1000V程度の電圧を印加することでガラス中のアルカリを酸素とナトリウムに分離し、界面において酸素とSiを接合させる技術。
2つの融合が解決策になる
従来、電子回路からなる半導体と、センサ素子からなるMEMSは、個別に製作し、最終工程で1つのパッケージの中に実装するのが通例である。
「貫通電極により半導体の3次元化は加速すると思います。またMEMSは、材料が限定されますが、すでに3次元積層化の方向に動きつつあります。この2つが融合することで、新たな高機能デバイスがぞくぞく出現するのは間違いありません。また、ウェハ同士で接合するWOW(ウェハオンウェハ)で、パッケージまで完成させることができれば、大きなコストダウンにつながるでしょう」
山内社長は、ここに新たな付加価値が生まれると考えた。
「3次元積層化のいいところとして、既存の半導体製造ラインで流せることがあげられます。ウェハやチップの積層装置だけ新たに設備投資するだけで実現できます。また、最後の実装工程としてウェハレベルでパッケージできれば、今の後工程と呼ばれる組み立て工程はほぼ不要となり、画期的な削減が達成できるでしょう」
新たな開拓分野の目標は決まった。しかし3次元積層化には、いくつかの難しい課題があった。この技術で大きな壁となっていたものがアライメント(位置決め)である。
「3次元積層化」では電極ピッチの微細化にともない、ウェハ同士やウェハとチップ、チップ同士を、理想的には半導体配線ピッチまで、寸分のズレなく積層しなければならない。現在の半導体製造ラインの中のフォトリソグラフィ※2 工程で使用している露光装置(ステッパー)であれば、物質と物質を接触させるわけではないので、平面方向の2次元的なアライメントで済む。一方、2枚を貼り合わせて加圧する接合においては、それに高さとあおり方向の軸を加えた3次元的なアライメントが必要。今までは半導体の工程には存在しなかった、“物理的な接触”が必要で、その接触によるわずかな位置ずれが、アライメント精度を悪化させる致命的要因と考えられていた。それは、実績のない非常に難易度の高い技術である。
さらに前述したように、MEMSで要求される真空封止を伴う接合では、高温加熱による陽極接合技術しかなかったため、異種材料接合による熱膨張差や、ガス発生の問題を避けて通るわけにはいかなかった。
「シリコンを材料とする半導体ウェハも含め、異種材料のウェハ同士を貼り合わせるには、熱による材料の伸びを抑えるために低温接合プロセスは必須です。さらに、半導体製造ラインでは、ウェハの大口径化が進んでいます。高温ではウェハを保持するステージに熱膨張によるうねりが生じ、強い圧力を、大口径のウェハ全体に均等にかけるのは非常に困難で、大きくなればなるほど難しくなります。つまり解決するには、低温、低加圧での接合プロセスが必要となります」
「高精度の3次元アライメント」、「低温、低加圧接合」という“夢の技術”に取り組んできたのが、山内社長率いるボンドテックなのだ。
※2フォトリソグラフィ(Photolithography)
感光性の物質を塗布した物質の表面をパターン状に露光すること。 露光された部分とされていない部分からなるパターンを生成する技術。
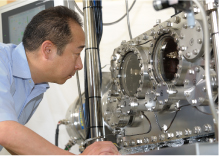

「常温接合」という足がかり
大手メーカーに勤務していたとき、とある学会で1人の人物を紹介される。表面活性化による常温接合技術の第一人者、東京大学の須賀教授。そのとき初めて、「超真空中常温接合」という技術を知った。半導体の金属電極を利用しての接合では、ハンダからなる合金物質を加熱溶解し、電気的な接合も行う拡散接合技術がよく知られている。ところが、須賀教授の技術を使うと、熱を加えることなく常温で、金属同士や異種材料同士をくっつけることができる。
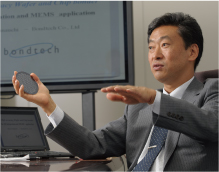
「物質の原子には、“握手”に例えられるような原子レベルの結合手を持っていると考えて下さい。物質内部では原子が持つ手と手がしっかりと結びついて離れず安定しています。またその表面は、空気中の酸素原子や有機物と手を結び酸化膜などとなって安定した状態を保っています。須賀教授が開発した常温接合は、“表面活性化技術”により表面の結合手を出させることで実現します。やり方は、材料同士の接合面にアルゴンの高速原子ビームをぶつけ、表面の酸化膜からなる原子やごみをはじき飛ばして結合手を露出させて活性化します。わかりやすく言えば、原子に結合手を出させた状態で、物質の表面同士を重ね合わせ、接合するというものです」
この技術を使えば、異種材料間でも熱膨張のない高精度の接合が可能となる。また、金属だけでなく、シリコンやサファイヤなど色んな物質を直接的に接合できる可能性がある。ただし、完全な常温環境で接合するためには露出させた結合手と結合する分子が存在しない、10-10乗Torrという超高真空環境下で行う必要がある。それはほぼ宇宙に近い「超高真空」と呼ばれる状態に匹敵する。超高真空の環境を用意するためには、ほぼ3日を費やして接合するための特別な部屋(チャンバー内部)から空気を抜きながら、さらに部屋のまわりを高温でベーキング(加熱)する必要がある。量産ラインで使用することを考えると、この超高真空環境がネックとなる。一方、量産化する上では必ずしも常温にはこだわる必要はなく、少々の低温加熱や加圧をすることで現実的な量産化ができれば問題はないと考えられる。そこで、常温接合技術を量産化に適合させるべく真空度を軽くし、低温で加熱する、さらには大気中でも接合できる表面活性化接合技術の開発に取り組んだ。
壁をこじ開ける
その方法は次のようなものだ。1つめにはまず材料を接合面が酸化しにくく、付着物が付きにくい性質を持つ金や銅に限定することによって、低真空化が実現可能となる。数Torrの真空度で扱えるプラズマが発生するレベルの処理で表面活性化することができる。金に限定すれば、表面活性化後1時間以内であれば大気圧中でも接合が可能であることがわかった。
さらに量産化に向けては、必ずしも常温、無加圧にこだわる必要もなく、多少の加圧や150℃以内の低温加熱により再付着物層を除去して強固な接合を得ることができた。この方法であれば、数Torrという低真空や大気中、低温、低加圧プロセスでの接合が可能となり、電極やMEMSの封止接合にも応用できた。また、2つめにシーケンシャルプロセス※3 を用いたプラズマ表面活性化により、シリコンやガラス、酸化膜付ウェハを低温、低加圧、大気中での接合を実現することに成功した。
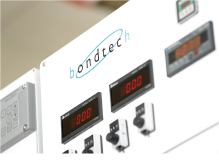
3つめには従来の陽極接合の原理とシーケンシャルプロセスを融合したハイブリッドボンディング※4 と呼ぶ新しい実装方法の提案で、従来の陽極接合に比べて低温、低ガス化を実現した。静電力によるボイドレスで、低温、低加圧、かつ短時間での接合に成功した。
さらに4つめには、従来の超高真空中での原子ビーム接合も改良を加え、大面積の接合も可能で、さらに真空度レベルを下げ、より扱いやすくすることができる方法を開発した。
そして山内社長は、もう1つの課題、アライメント技術においても従来とまったく違った発想によって壁をこじ開ける。これまで、ウェハ上に回路を露光する場合、ステッパーと呼ばれる高額な装置が使われていた。
サブミクロンオーダーの高精細な回路を焼き付けるために、微細な振動すら許さない高精度の耐震構造が必要であった。大きく重い御影石などの石定盤を、装置の下に敷いて振動を防ぐ。また熱膨張による誤差を防ぐために、装置の温度を一定に保たなければならない。非常に厳しい温度コントロールができる環境下での運用が必要だ。つまり従来の微細化のための装置設計の発想は「下から積み上げて精度を維持する」という発想だ。
しかしこの方法だと大掛かりな構造となってしまい、量産用のステッパーは1台何十億円という高額な装置となってしまう。一方、ボンドテックのアライメント手法は、「下から積み上げて精度を維持する」のではなく、「位置合わせをしたいものを直接把握し、それを接合直前にコントロール、つまり対象物を直接微小に動かせば良い」というごく当たり前であるが、新しい発想からなる。対象物をチャンバの外の離れた位置から赤外線カメラで撮影し、独自開発した「マジックビジョン(MagicVision)」という画像認識システムで赤外線透過画像を高精度に認識する。さらに、対象物が接触する直前に6軸方向を位置制御するこれもまた特殊なピエゾアクチュエータ※5で、ずれた寸法量を微調整し、数十ナノレベルの位置決め精度を実現した。また、真空チャンバ内では使用することが不可能なベアリングを使用しないコンパクトな機構から、超高真空チャンバ内にもアライメントするユニットを搭載することが可能で、大気中と同じ精度を維持することができるのである。
山内社長が開発した装置は接合後で0.2μm。これにより、これまでアライメントが難しかった超微細配線同士の接合が十分に可能となった。現在は一桁下の数十ナノレベルの開発を行っている。そして驚くべきことに、装置1台あたり2,000万円から、量産向けの完全フルオートシステム開発でも2億円以下という価格帯を実現した。
※3シーケンシャルプロセス
Siやガラスを大気中で接合する方法。プラズマ処理により界面にOH基を付着させ、低温アニーリングすることで強固に接合する。酸素プラズマのあとに窒素ラジカルを連続処理することで加熱温度をSiで100度以下(ガラスで200度以下)に下げる技術を、東京大学須賀教授が開発した。
※4 ハイブリッドボンディング
前処理として、MEMSの封止に使われる陽極接合と表面活性化を併用し、低温、ボイドレス、低アウトガスを達成。
※5 ピエゾアクチュエータ
ピエゾ圧電効果を応用した位置決め素子。
2つの革新
現在、ボンドテックではナノレベルの微細回路を転写するナノインプリント装置の開発も手がけている。
「これまで使われてきた半導体製造工程のフォトリソグラフィ※2 技術では、さらなる微細化に物理的な限界があり、ナノインプリント方式に移行すると思います。当社のナノインプリント装置は、高精度なアライメント技術を生かし、UV硬化樹脂の性質を応用した常温インプリント方式で、さらなる微細化を実現した電子回路を転写することが可能です。半導体製造ラインの最初の工程であるフォトリソ工程がナノインプリントリソグラフィ※6 工程に置き換わり、半導体製造工程の最後にウェハを貼り合わせる3次元積層接合方法を追加するだけ。既存の半導体設備を生かしながら、我々の開発する設備を追加するだけで次世代の生産工程が誕生し、高性能な3次元半導体素子や半導体とMEMSの融合デバイスを生み出すラインに刷新できるのです。当社は、この2つの革新のキーとなる技術を押さえています」
ボンドテックの接合装置で接合できる材料が広がり、MEMSと電子回路の融合も当たり前のこととなる。すでに半導体とMEMSは製造ラインの兼用化が進んでおり、近い将来切り替わっていく可能性は高い。それだけでなくボンドテックは、現在の大手ステッパメーカーに取って替わる可能性をも秘めている。今後、バイオ、メディカル、自動車、ロボットなど、さまざまな分野に応用が進み、今は想像もできないような機能を持ったデバイスができるかもしれない。つまり半導体製造はもちろん、我々の生活も大きく変わっていく可能性があるわけだ。
夢を追う、実現する
山内社長は言う。
「こうした開発には膨大な研究開発費が必要で、いつ回収できるか分かりません。私自身の人生をかける覚悟が必要です。社員の生活もかかっています。プレッシャーで押しつぶされても不思議ではありませんね」
ではなぜ、それに打ち勝つことができるのか。
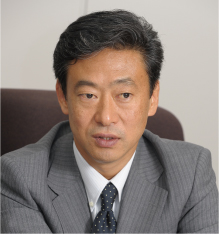
「ひとつは、“把握する”ということがプレッシャーを軽減してくれます。開発という仕事は、人頼りでブラックボックスが存在すると予想がつきません。すべてを把握して、自分の手の中で動かすことで、最悪の事態と最大の成果をリアルタイムに把握できます。そうすることでプレッシャーはかなり軽減できます。また、プロジェクトの最初と最後を押さえること。商品開発であれば、客先や市場からの要望と完成した商品の完成度を必ず自分で触って把握する。こうすることで、問題解決がすばやくフィードバックされる上に、そこから新たなアイデアも生まれてくるのです」
さらに、もっと重要なことがあると言う。
「もう1つは、かなえたい夢があることです。表面活性化接合技術、ナノインプリント技術を活用し、半導体とMEMSの融合デバイスの製造を可能とする、付加価値の高い製造システムを世に立ち上げること。日々革新的な技術を研究されている先生方の研究成果を具現化したいという夢があります」
淡々とした語り口調であるが、不思議と強い思いが胸に刺さってくる。夢への渇望をあらためて感じるのは、私だけではないだろう。
「当社は開発のスピードを生命線とし、社員が十名未満しかいないにもかかわらず、大企業なら3年はかかるこうした商品を、半年で開発しています。それをやり遂げているのは、志を共にしたメンバーの結束力と集中力、高い技術力がなせる技なのです」
夢は俊足である。捕まえるためには、走り続けなければならない。山内社長はこれからも半導体業界を全力で走り抜けていく。
「このスピードを武器に、高い技術をアイデアで差別化した知的財産を、次々に商品化していきます」
山内社長は、アイデアは夜眠っているときに生まれるという。
「仕事量をこなすのは昼間ですが、頭脳の使用率は表面の10%ほどだけのように思いますね。夜、浅い眠りのとき、無意識の中、問題解決の道を探ると、頭の奥から不思議とアイデアが浮かび上がるのです。そのたびに寝床から身体を起こし、枕元にあるメモ帳に書き留めていきます」
おかげで寝不足になることもしばしばだとか。山内社長は出張のたびに枕を持ち歩く。睡眠が一番の贅沢だという。
「社員や協力スタッフの努力に報いるためには成功しなければならない。そうした思いがあるからこそ、踏ん張ってこれたのです」
当面の目標はアプリケーションを1つでも多く立ち上げること。具体的な数字を聞きたくなるが、
「年商ですか?ひとつアプリケーションが立ち上がると年商100億ぐらいは自然とついてくると思います」
目標としているのは、そこではないようだ。
「これからも大手メーカーができないことをどんどんやっていきますよ」
半導体の変革という夢の足音が山内社長の耳に大きくなり、おぼろげだったその姿は、はっきり実感できることころまで来ているのかもしれない。