だれしも一度は手にしているだろう。最も身近な工具、ドライバー。
しかし、どのような思いを込めてつくられているのか、となると、意外と知られていないのではないか。
日本で初めてドライバーを量産した企業「ベッセル」は1916年創業の老舗、
今では国内ドライバー市場でシェア約60%を占める業界のトップメーカーだ。
ベッセル島根の田口二郎社長はいう。
「ネジがあって初めてドライバーも必要になるわけですが、両者の関係が一筋縄ではいかないのです」
ネジの凹に、ドライバーの凸。
微細で目には見えない、知られざる世界に迫った。
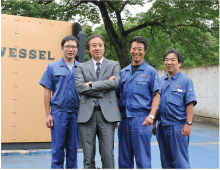
6割はオーダーメイドのビット
「当社は、“国内初”となるような取り組みを数多くしてきました。これまでなかった商品を開発することが、当社の生命線であり、使命だと思っています」
田口社長は力強く語る。
『VESSEL』。
英語で、「容器」「うつわ」などの意味があるが、もう1つ「大きな商船」の意味がある。商標をつくる際、創業者が財宝を積んだ宝船の夢をみて、「これは縁起がいい」とつけたのが社名の由来だ。
ベッセルは企業グループを形成しており、販売と営業を行う株式会社ベッセルのほかに、国内外に5つの工場をもち、それぞれが独立した株式会社となっている。そのなかで、柄が付いていない、先端と軸だけで構成されたドライバー用の刃先である「ビット」を製造しているのが、株式会社ベッセル島根である。
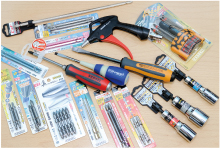
「ビットは、建設現場や自動車や家電、パソコンの生産ライン、半導体など、さまざまなところで使われ、多くが工業用です。当社製ビットで大ヒットとなった商品に『両頭ビット』があります」(田口社長)
ビットはエアドライバーなどの先端に取り付けて使われるが、これまで刃先は片方の端にあるだけだった。それを両端に付け、1つが使えなくなったら、もう片方でも使えるようにしたのが両頭ビットである。
この意表をついたともいえる大胆な商品は爆発的なヒットとなり、国内はもちろん、アジア地域も席捲。海外の売上げが3割も占めるベッセル島根の原動力の一つとなっている。
「ビットの規格品は800種類ほどありますが、規格品とは別に、年間1,200種類ほどのビットをつくっています。それらはすべてオーダーメイドの依頼です」(田口社長)
一般の人がドライバーをオーダーメイドすることはまずない。それなのになぜ各企業は、わざわざオリジナルのビットを必要とするのか。
実はここに、ネジとビットの“複雑な関係”が潜んでいるのだ。
“ふぞろいの”ネジ
身の回りに数多く存在するネジ。それらは、JIS規格によってすべてサイズが決められている。
一般的に使われるものは1~4番と呼ばれる大きさであり、数字が大きくなるほどネジのサイズは大きくなる。精密機械向けには大きい順から0、00、000がある。
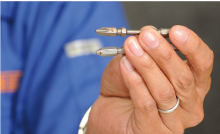
「基本的にはネジのJIS規格に合ったビットをつくれば大きな問題は起こらないはずです。ところが現実には、同じ規格サイズのネジでも、メーカーによって微妙に形状やサイズが違っていることがほとんどで、そればかりか同じメーカーであっても形が違う場合があるのです」(米澤工場長)
JIS規格に準拠してつくっているネジ。それがなぜこれほどまでにバラバラなのか。その理由の1つは製造方法にある。
「ネジの製造方法は非常にシンプルで、パンチと呼ばれる金型をネジの素材となる金属に押し付けネジの溝をつくります。つまり、金型の形をネジに写すだけのプレス成型です。そのため切削加工と比べるとどうしても精度が落ちてしまいます」(伊藤主任)
もう1つ大きいのが、各社の「品質基準」だ。金型は何度も打っていると摩耗する。品質基準が厳しいメーカーであればわずかな摩耗で交換するが、基準が緩い企業ではそのまま使い続けることもある。その場合、1ロット目はJIS規格とほぼ同じサイズだとしても、10万ロット目では摩耗して形も変わってしまうのだ。
一般向けであれば、ネジの形とドライバーの形が多少合わなくてもさほど問題にはならない。しかし工業用の場合、わずかなサイズのズレも許されない。その理由は、製品の品質、生産性に大きな影響を与えるからだ。
「お客様からの要望でもっとも多いのは耐久性です。たとえばネジ締め作業が、ラインに組み込まれているような場合、ビットが磨耗すると、交換のためにラインが停止してしまうことがあります。また、精密さを要求されるハードディスクなどのメーカーからは、ビットを回して先端が振れる幅(ビット精度)を0.02mm以内に抑えてくれという要望が出たこともあります」(米澤工場長)
高耐久性が求められ、わずかなブレも命取りなる製造現場。だからこそ各企業はわざわざオーダーメイドでビットの製作を依頼してくるのだ。
「このネジに合ったビットをつくって下さい」
多くのメーカーが、製造現場で使っているネジを手に、ベッセル島根にやってくる。
たとえJIS規格に合っていないネジであっても、渡されたネジの形を正確に知り、それに合った形のビットをつくれば問題はクリアできる。
「でも」と田口社長はいう。
「『ネジの形を知ること』が、難しいのです」
ネジの本当の形を、知りたい
ビットは、我々が想像する以上にさまざまな工夫が施されている。
ネジにビットを入れて回そうとすると、回転の力によってビットが浮き上がって溝から出てしまう現象(カムアウト)がある。これが発生するとネジを痛めてしまうため、先端部分に刻みを入れ吸い付きやすいようにすることがある。
「ネジを締めきったときにはビットに強い衝撃が発生します。その際に衝撃を和らげるためにビットの中央部を細くすることもあります」(米澤工場長)
また、ビットで大事なのは「硬さ」と「粘り」だという。表面が硬ければ摩耗しにくく、全体的に粘りがあれば衝撃を吸収しやすいからだ。
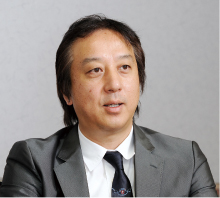
ベッセル島根では、ビットの素材をNC旋盤やフライス盤で製品形状に加工した後に、日本刀の製法と同じように焼き入れを施している。プラズマ真空炉を使い、焼き入れを行うことで表面を高硬度、中を低硬度にし、「硬さ」と「粘り」を持たせることができるという。そして、こうしたビットづくりのノウハウのなかで、もっとも基本かつ重要となるのが「ネジの溝と同じ形にする」ことだ。そのために、何よりまず把握しなければいけないのが「ネジの溝の形」である。
ネジの溝の形を知る──。
ベッセル島根ではさまざまな道具を使い、形を探ってきた。接触式のコントレーサー(形状輪郭測定器)、マイクロスコープ、投影機……。だが、こうした測定器を使ってもなお測定できない箇所があった。
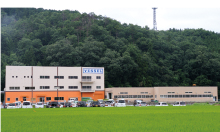
「ネジ頭部の凹んだ部分でも、ゆったりとした傾斜であれば測定できますが、極端に角が落ちているような急勾配な面では正確な数値が出ないんです。そのため、ビットをネジに当ててみて噛み具合をみるという、職人的なカンに頼らざるを得ない部分がありました」(糸賀班長)
ビットの試作品をつくってはネジにはめ、合っているか確かめる。ダメなら再度つくり直さなければならない。
何度も何度も繰り返される作業。そしてそれは、これまでずっと続いてきた作業でもあり、いまの測定体制が続くかぎり今後も間違いなく繰り返される作業でもある。
しかし田口社長はある決断を下す。
探し続けたネジの溝の形がわかる測定装置
田口社長は、ネジの溝の形を計測するための測定装置を、徹底的にリサーチする。
インターネットや展示会などで測定装置を探し、使えそうな機種を複数ピックアップ。次々とネジを測定していった。もっとも知りたかったのは「溝の奥まで測れるか」である。
「測定装置メーカーに依頼して何度もネジを測定しましたが、いずれも満足できるものではありませんでした。どうしても溝のいちばん奥の部分が測定できないんです」(田口社長)
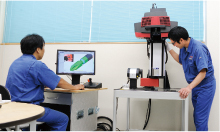
測定装置をリサーチしはじめてすでに半年以上。そんなとき、社員の1人が名古屋の展示会で出会ったのが3次元デジタイザ『ATOS TripleScan(エイトス トリプル スキャン)』だった。名古屋まで通ってテストを開始。ネジのサイズを変えて再度テスト、テスト、テスト。
2011年春、ベッセル島根ではこれまでテストをした測定装置を一覧表にまとめ、最終的な検討に入る。選んだのは『ATOS TripleScan』。
微細な形状を正確に把握でき、溝の奥まで測定できたことが決め手となった。
ビットとネジの形状を様々な観点から検査できることも導入のポイントになったという。
永遠につぶれないビットを
ついにつかみ始めた「ネジの溝の形」。
ベッセル島根では「変化」の胎動がすでに生まれている。
「ネジの形がわかれば、設計する場合に何を目ざしていけばいいのかが明確になる。手探りだった部分がはっきりするのは、設計担当からすると非常に助かります」(糸賀班長)
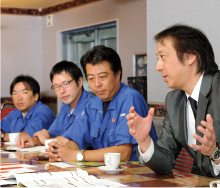
田口社長が期待しているのは、クレーム時の対応がしやすくなることだ。
「お客様から『ビットが合わなくなったぞ』とクレームが出ることがあるんです。そのときに納めたビットがデータ化してあれば、製造現場で使われていたビットを測定して2つを比較すれば、問題がビットかネジなのかがすぐにわかるはずです」
すでに3次元デジタイザシステムを使って、シミュレーションのテストも行われている。
「ネジとビットの両方の計測データを合わせて、どこが干渉するのか、遊びがありすぎないかを事前にチェックしています。通常、2つを接合すると接合部分は見えませんが、シミュレーション上でなら見ることができます」(米澤工場長)
田口社長は語る。
「まず、世の中のネジの溝の形の主流がどこにあるのかを把握したいと思っています。それに合った規格品のビットをつくることで汎用性が出てくるからです。そしてできれば、永遠につぶれないビット、あるいはつぶれても再生できるビット、そんな世の中でまだ誰も成し遂げていないことを実現できたらと思っています」
2011年、田口社長はスローガンに「ネバーストップ、挑戦をやめない」を掲げた。
ネジとドライバーのわずかな接点。そこに夢と工夫がいっぱい詰まっている──。